Manufacturing Process
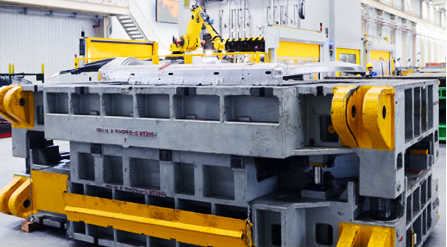
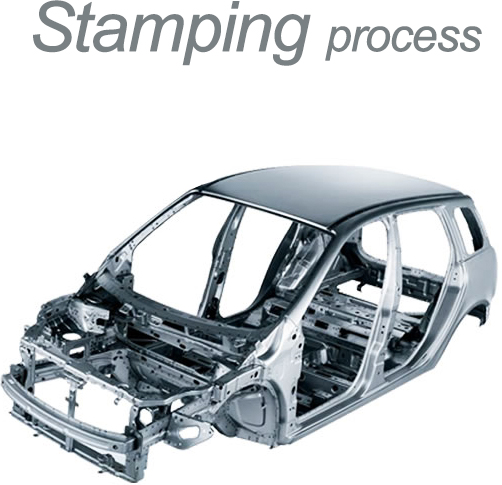
We use large automatic stamping line and robot automation to effectively guarantee the safe production. High production efficiency, stable product quality and low production cost are the results of such process.
Non-swing shear technology is adopted in the uncoiling and material unloading process.
6300 tons mechanical longitudinal beam press, 5000 tons longitudinal beam hydraulic press, steel uncoiling and unloading line, longitudinal beam roller press line, 800, 1250, 3000 tons presses, CNC punching line, frame riveting connection line, frame painting line, frame spray line and other large production lines are adopted.
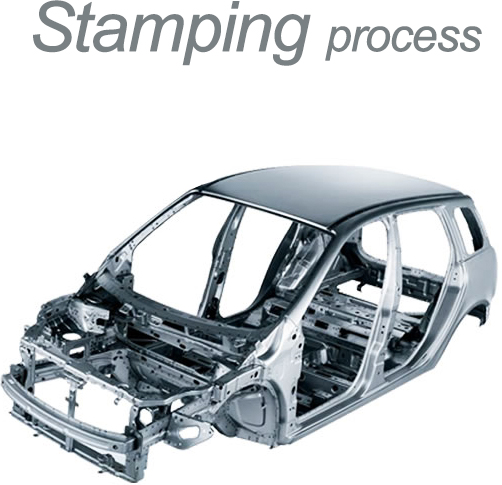